The answer to the problem of uneven hardness that was caused by the die-casting process for zinc all
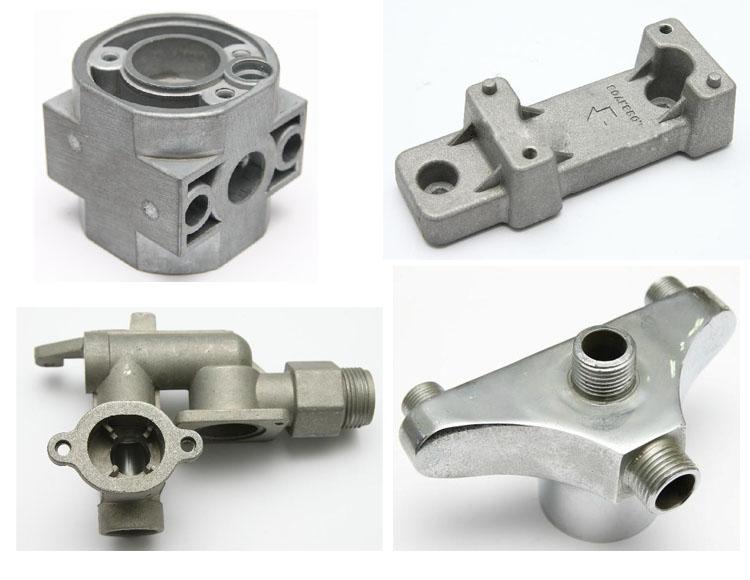
The heat treatment of zinc alloy die-casting typically involves the use of the carburizing and quenching processing technologies. Uneven hardness is a typical example of a problem that can occur during the manufacturing process of heat treatment.
The primary reason for the uneven hardness
The primary reason Plating for the uneven hardness.
1) The contamination of the environment by commercial surfaces
The carburizing and quenching heat treatment not only stipulates the cleanliness level of the surface before the heat, but it also prohibits the surface from becoming contaminated by the surrounding environment during the carburizing process that takes place inside the furnace.In the process of carburizing, the reasonable adsorption of carbon will be negatively impacted if there are oil stains and rust present prior to heating..
During the process of carburizing, it is essential to protect the uniformity of carburizing from the potential damage caused by carbon black agglomeration. The uniformity of temperature control in the furnace can be thrown off by a number of unforeseen circumstances, such as the airtightness of the furnace, the common failures of the side doors, the common failures of the radiant tubes, and materials that become stuck. In the portion of the furnace that has a low carbon potential, the carburizing work capacity is decreased. Additionally, the problems of a shallow infiltration layer and low hardness are likely to manifest themselves in this portion of the furnace.
3) Inadequate levels of cooling
The quality of the quenching will be affected by the cooling properties of the quenching oil as well as its level of cleanliness.The problem of uneven hardness is caused China die casting manufacturer by common flaws in the oil stirring device as well as by an inappropriate loading method, both of which will have an effect on the quenching and the refrigeration processes.
Before beginning the heating process, there shouldn't be any rust or oil stains. The initial thermal resistance only requires that the measurement verification be performed once per year. This stipulation should be adhered to. In order to guarantee the precision of the processing temperature, the main temperature control at our company is now calibrated with a thermal resistance that has a high level of sensitivity.
Enhance the quality inspection of raw materials such as industrial methanol and propane gas, as well as eliminate the damage to the dependability of the carburizing atmosphere that is caused by moisture and other residues in raw and auxiliary materials. During normal operations, the degree of agglomeration of carbon black is identified, and concurrently, the reason for the abnormality of carbon black is investigated. Check the tightness of the furnace on a regular basis, paying particular attention to the middle door; check the tightness of the middle door at the appropriate intervals to guarantee that the temperature can be maintained at a consistent level. During the process of quenching the components as they move from the back chamber to the pre-processing chamber, the posture will occasionally stop, and the components will be fed into the oil with a delay time in between each step. At the moment, it is necessary for a certain number of individuals to be present during the quenching process in order to keep an eye on the posture status and alarm records of the various pieces of machinery and equipment. The application of each radiant tube needs to be monitored, in addition to the maintenance that is performed on the radiant tubes themselves. In the event that the radiant tube exhibits abnormal behavior, it is possible to remove and immediately replace it, and the processing technology can be modified at any time. Inhomogeneity in carbon potential can be checked indirectly by examining the degree to which parts have been carburized. After any time the process is altered or the equipment is overhauled, the carburizing uniformity test is required to be performed per our specifications.
To ensure that the quenching oil can effectively dissipate heat, it is important to check the cooling properties of the oil at the appropriate time. The anti-carburizing architectural coatings that are chosen should not pollute the quenching oil that is extracted from the surrounding environment. These products are going to be thrown away. Among these are the most typical issues Metal Plating that arise during the process of die casting. Die-casting an aluminum alloy possesses a high compression resistance to the surface of the casting process. These products are going to be thrown away. Air bubbles are the most common issue that arise during the process of die casting.
Technology for the treatment of aluminum alloy surfaces and for decorating them has zinc alloy die casting advanced rapidly in recent years; as a result, the electroplating surface is very shiny. It's not that we are forced to find solutions to these problems; far from it.
- Sanat
- Doğa
- El sanatları
- Dans
- İçecekler
- Film
- Kondisyon
- Gıda
- Oyunlar
- Bahçıvanlık
- Sağlık
- Ev
- Edebiyat
- Müzik
- Networking
- Diğer
- Parti
- Din
- Alışveriş
- Spor Dalları
- Tiyatro
- Yaşam