The underlying cause of flange leakage as well as the characteristics of the flat welding flange are
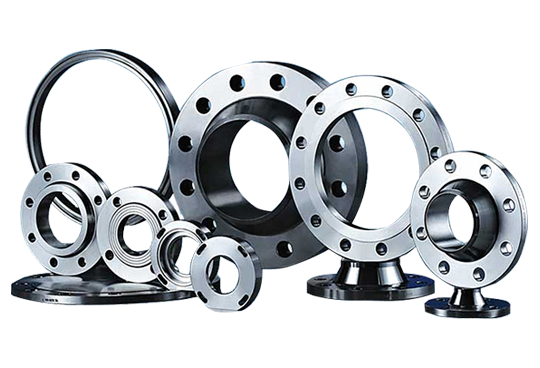
In this particular instance, any flange will do as long as it has the appropriate size. However, when designing the component, it is essential to decide whether the integral flange or the loose flange should be used. When making this decision, it is important to take into consideration the Flange level of integrity possessed by the flange ring and the straight cylinder section. In comparison to the neck butt welding flange, the flat welding flange has a construction that is more straightforward and a design that is more straightforward. On the other hand, the flat welding flange's rigidity and sealing performance are not even close to being as good as those of the neck butt welding flange. When contrasting the flat welding flange with the neck butt welding flange, this observation is especially apt to be made.
It was necessary to reduce the size of the compact flange in order to accommodate the smaller diameter of the seal. The flange gasket has been replaced with a sealing ring so that the sealing surface can be machined. This has the effect of reducing the cross-section of the sealing face, which is a positive development. This step was done stainless steel flange to make step two easier. This was done so that the surface of the seal could be machined. This step was taken in order to facilitate step two. A flat welding flange not only ensures that the joint will not leak and will have excellent sealing performance, but it also reduces the amount of space that is required for the joint. This is because a flat welding flange is more efficient in the use of space. In addition to this, a reduction in the total amount of weight that must be supported by the joint is also necessary.
As a consequence of this, the diameter of the bolts will need to be enlarged in order for them to be usable. It is impossible to screw the nuts in any further because there is no more room. This is because nuts with larger diameters need to be mated with bolts that are larger in diameter. Bolts with larger diameters need to be used with nuts that have a larger diameter.
On dual-phase steel flanges, polishing processes such as hand-polishing, mechanical polishing, chemical polishing, and electrochemical polishing are all viable options for finishing the surface. Because this procedure involves polishing and cleaning, some chromium and phosphorus will be released into the waste water as a byproduct of this step. Because of the microscopically inconsistent surface of the dual-phase steel flange, the microconvex part on the surface dissolves preferentially, and the rate of dissolution will be higher than it would otherwise be. The roughness that was previously present on the surface of the duplex steel flange has been smoothed out, and a smoother surface has been created.
3. This can be accomplished by filling in any surface scratches or pores that may exist. It has an excellent resistance to stress corrosion cracking, particularly in environments rich in chloride ions, in addition to possessing sufficient plasticity and toughness for this forming. This is especially true in environments where there is a high concentration of chloride ions. Flanges made of duplex steel have yield strengths that are more stainless steel flange than twice as high as those made of austenitic stainless steel. This is especially true in environments where there is a high concentration of chloride ions. In addition to this, it is possible for it to form under the influence of stress without fracturing, which is particularly useful in circumstances in which there is a high concentration of chloride ions in the surrounding environment.
1. As a consequence of the corrosion effect, the gasket goes through a series of chemical transformations; the corrosive medium makes its way into the gasket; the gasket starts to become pliable and loses its compressive force; as a consequence, the flange begins to leak; 2. In addition to this, it will result in the sealing surface of the sealing surface becoming deviated, which will significantly increase the likelihood that there will be a leak. The corrosive medium breaks through the gasket, which will result in a lessening of the tension that is already present between the two flanges.
3. When the flange clearance is too large, it will cause external loads (such as axial loads or bending loads), which will cause the gasket to be impacted or vibrated, lose the compression force, and gradually lose the kinetic energy of the seal, which will cause the flange to leak. Flange leakage will take place whenever the load pressure of the gasket is higher than the pressure of the internal medium. When the flange clearance is too large, it will cause external loads (such as axial loads), and the solution is not overly difficult to find. Because of the pressure that is present, the preferred method for installing flanges is the butt joint of two adjacent flanges; however, the temperature of the pipeline will change during the manufacturing process of the system after it has been introduced. Because of this, the butt joint of two adjacent flanges is not always the best option.
6. A wrong hole occurs when the pipe and the flange are concentrically aligned with one another, but the space between the two bolts is larger than the bolt hole. This gap allows the medium to leak through the pressure. The thermal expansion and contraction of the fluid medium will also cause the bolt to expand or contract.
- Art
- Causes
- Crafts
- Dance
- Drinks
- Film
- Fitness
- Food
- Jocuri
- Gardening
- Health
- Home
- Literature
- Music
- Networking
- Alte
- Party
- Religion
- Shopping
- Sports
- Theater
- Wellness