Utilization of advanced composite materials in aerospace products Technical specifications for the a
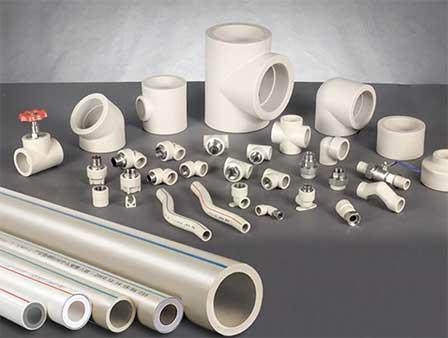
Composite materials that provide additional physical properties in addition to their mechanical properties are known as functional composites. These properties can include chemical and biological properties. Functional composite materials have a significant amount of design leeway, and their functionality can be incrementally improved in the following steps: function, multi-function, intelligence, and intelligence. In order to obtain not only the properties of the original material, but also some new properties or better performance than the original material, functional composite materials combine and match materials with electrical, acoustic, optical, thermal, and magnetic properties according to different applications.
The confrontation and accuracy of weapons have seen significant improvements as a result of modern, high-tech conventional warfare. The fortification and tracking of future smart weapons, stealth weapons, electronic warfare weapons, online machining services laser weapons, and new concept soft-kill weapons will make functional materials an important technology. The growth of the national defense industry, along with the production of new weapons and equipment, will be greatly influenced by the research and development of cutting-edge technologies involving functional composite materials. In the aerospace industry, including aircraft, helicopters, aerospace products, and ships, advanced composite materials are frequently used.
1. The increasing use of composite materials in aircraft and their trending development
They have made significant progress across the board in a variety of aircrafts ever since the introduction of cutting-edge composite materials.They have now developed into the fourth largest aviation structural material, joining the ranks of aluminum, steel, and titanium.It has excellent resistance to fatigue and the ability to reduce vibrations, it has a designable model, and it has a concealed model that absorbs waves. This makes it the ideal choice for aircraft.The percentage of composite materials utilized in the construction of the airframes of modern and advanced aircraft is growing.After going through a number of stages of development, it has finally accomplished the application of non-load-bearing and secondary load-bearing components to the primary bearing force of the tail, and then to the primary bearing components of the wings and the fuselage.This is a requirement not only for the performance of the aircraft, but also for the success of businesses and competition in the market.
Composite materials are gradually becoming more prevalent in the aviation industry as a result of the consistent development of science and technology. These materials are also extensively used in the expansion of modern aviation. It has important practical significance for the research on composite material structure repair technology because composite materials have become an important part of the structures of modern aircraft. Furthermore, the mechanism by which composite materials are damaged is distinct from the mechanism by which metals are damaged.
In general, composite materials have drawbacks such as low interlaminar strength, poor lateral performance, and poor compressive capacity. Composite materials also tend to be expensive. Cracks, notches, delaminations, and holes are some of the most common types of structural damage that can be caused to an aircraft, and the most common cause of this type of damage is impact damage. Reduce the static and dynamic load performance of composite materials, which will, in extreme cases, pose a direct risk to the flight safety of the aircraft. Maintenance of composite aircraft structures is becoming increasingly important as the percentage of composite materials used in aircraft structures continues to rise. It is imperative that research and development of repair materials be sped up, that continuous learning of new technologies take place, and that progress be made toward high quality, high efficiency, and low cost. develop.
2. The use of composite materials in online cnc machining service helicopter construction and the requisite technical specifications
Helicopters that are constructed with modern composite materials have the potential to lose weight while simultaneously increasing their resistance to impact.At the moment, domestic helicopters use an advanced composite material for the blades of the rotor system and a titanium alloy spherical flexible main propeller hub. Additionally, the body of the helicopter uses composite material for part of its structure, and the use of composite materials can account for up to fifty percent of the aircraft as a whole.In the not too distant future, the proportion of composite materials found on helicopters will reach between 70 and 80 percent, and there may even be aircraft made entirely of composite materials.
3. technology for the use of composite materials in the structure of aerospace products
Aerospace products use a large number of different advanced composite materials, such as glass fiber, glass fiber reinforced plastic, carbon fiber, and other products. These materials, along with others, have contributed to the lightweight design, low cost, high heat resistance, and high performance of missiles and rockets.When it comes to the construction of missile bodies, wings, tails, radomes, air intakes, and other structural components, advanced composite materials are almost always used.Within the realm of launch vehicles, advanced composite materials have the potential to be utilized in the production of solid engine casing structures, rocket fairings, instrument cabins, interstages, engine nozzle throat linings, satellite brackets, cryogenic tanks, and other components.Because advanced composite materials offer significant performance advantages in addition to the potential for lightweight capabilities, these materials have found widespread use in the field of launch vehicles and missiles.It is anticipated that carbon fiber composite materials will be utilized in this sector in the not-too-distant future for an extended period of time in order to effectively reduce the weight of rockets and missiles and improve their performance in combat.The number of applications will be increased even further.
The utilization and demand for marine composite materials comes in at number four.
Composite materials for ships, particularly those used in the construction of the hull, are almost exclusively composed of polymer-based composites.Composite materials can be broken down into two distinct categories, based on their structures: laminate and sandwich structures. Within each of these categories are three essential composite components: reinforcement material, resin, and core material.According to the various load-bearing parts, marine composite materials can be categorized into three different types of structures: primary load-bearing structures, secondary load-bearing structures, and non-load-bearing structures.Structure, damping, acoustics, stealth, and protection are the five distinct categories of materials that can be subdivided into this category based on its function.The use of composite materials in marine applications offers a number of significant benefits.The primary challenges that prevent composite materials from being used in marine applications are the need for accelerated design and development of composite materials as well as the formulation of unified design standards.
Demand in the Industry and Its DevelopmentDeveloping Technologies for Ships Made of Composite Materials
Demand in the Industry and Its DevelopmentDeveloping online machining services Technologies for Ships Made of Composite Materials.
After the opening of the Arctic route, the requirements for the thermal insulation online machining services performance of the ship's hull, particularly the superstructure of the ship, were put forward. The use of steel plates alone was unable to meet the requirements because steel plates do not provide adequate insulation. This issue can be remedied by constructing the ship's superstructure out of composite materials instead of traditional wood. And one could make an industry out of this. There are undoubtedly a great number of challenges to overcome on the technical front here.
- Sanat
- Doğa
- El sanatları
- Dans
- İçecekler
- Film
- Kondisyon
- Gıda
- Oyunlar
- Bahçıvanlık
- Sağlık
- Ev
- Edebiyat
- Müzik
- Networking
- Diğer
- Parti
- Din
- Alışveriş
- Spor Dalları
- Tiyatro
- Yaşam