Broken taps or screws during the processing of hardware parts
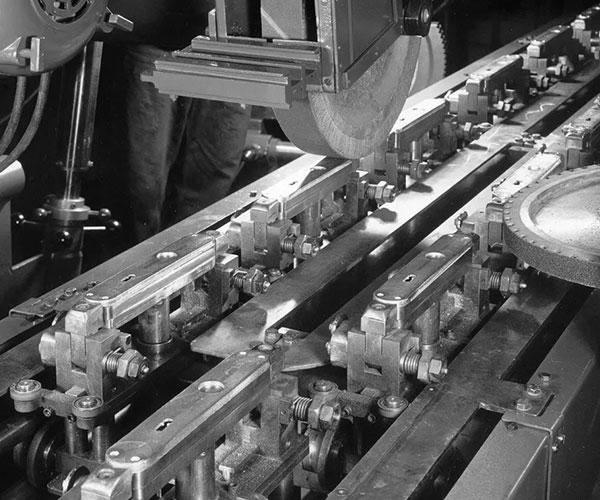
You must have been exposed to such a terrifying account given your position as a practitioner in the machinery industry. When processing hardware parts, how do you get the screw and the screw head to break apart at the same time?In point of fact, there are quite a few approaches, and we are going to take a cursory look at a few of them today.
Pour some lubricating oil on the fracture surface, then use a sharp hairpin or chopper to knock out small pieces slowly while moving in the opposite direction. Occasionally, pour some iron on the surface. This is the method that is most frequently used in the workshop; however, it may no longer be suitable for threaded holes that have diameters that are too small or broken taps that are too long. The principle behind breaking the tap extractor with a specialized tool is that the workpiece and the tap are connected to the positive and negative electrodes respectively, and the electrolyte is poured in the middle. This causes the workpiece to discharge and corrode the tap, and then the auxiliary needle-nose online cnc machining service pliers are used to remove it, which causes very little damage to the inner hole. The process can be repeated as many times as necessary to break the tap extractor.
Weld a handle or hexagonal nut on the fractured section of the tap, and then gently reverse it; while the tap is being used to process metal parts, if the screw becomes lodged in it, try to place the steel roller on the tap crack and tap it slowly with a small online cnc machining service hammer, the tap is relatively brittle, and finally knock it out into slag, or more simply, directly drill the threaded hole of the broken tap, and then re-ream and tap itMake a slot in the section of the broken tap, and then use a screwdriver to tighten it in the opposite direction.
Weld the threaded hole in the spot where the broken tap was, then grind the weld down until it's flat, and then re-drill the hole. Even though it is difficult, it is possible to drill slowly through it. When re-drilling and tapping, it is recommended to switch back to the original threaded hole if it is possible to change the threaded hole in the first place. Drill the threaded hole of the broken tap to a larger size, then insert a wire screw sleeve or pin or online milling service something else, then weld and smooth it, and re-drilling and tapping can be performed in a manner that is functionally equivalent.
An electric pulse could be utilized to put an end to the spark or the wire cutting. In the event that the hole is damaged, it is possible to ream the hole and add a wire screw sleeve. This approach is not only less complicated but also more practical. Regarding the coaxiality, put it out of your mind for the time being unless the coaxiality of the threaded hole in your equipment has a direct bearing on the quality of the device. You could, for instance, make a simple tool and insert it into the chip groove of the broken tap section at the same time, then carefully pull it out in reverse. Alternatively, you could screw two nuts onto the broken tap with a square tenon, insert a steel wire into the empty groove of the broken tap and the nut, and then proceed with the repair. In order to remove the broken tap, you will need to use the hinge lever to pull the square tenon in the direction of the exit. The central concept behind this method is to connect and break the chip flute of the tap, and then to make a wrench specifically designed for breaking the wire out of the steel wire by using the steel wire as a steel needle. It stands to reason that a suitable tool wrench should be fabricated in the event that a wire is broken in the workshop on a regular basis.
Nitric acid can corrode high-speed steel taps without causing the workpiece to be destroyed, which makes it ideal for the production of precision hardware parts that are customized in small batches. Although the screw was removed after a lot of hard work, the hole was scrapped and a larger hole was drilled for tapping instead of using the original hole. The tapping should be directly welded, and then a small hole should be drilled in the center of the large screw to be tapped. However, the problem with the internal metal structure after welding can be difficult to tap into.
What are the prerequisites for the different CNC machining processes, and how are they divided?
What are the prerequisites for the different CNC machining processes, and how are they divided?.
When dividing the process of CNC machining, it is necessary to have a flexible grasp on it in accordance with the structure and craftsmanship of the part, the function of the CNC machining center machine tool, the number of CNC machining operations that are contained within the part, the number of installations, and the production organization of the unit. It is also recommended to adopt the principle of process concentration or the principle of process dispersion, which should be determined according to the actual situation but must be reasonable. Whether to adopt one of these principles is something that should be determined according to the actual situation.
Tool centralized sorting method, this method is to divide the process according to the tools used, and to use the same tool to process all of the parts on the part that can be completed. Tool centralized sorting method. In order to cut down on the amount of time spent changing tools, condensing the amount of time spent waiting for work to be done, and eliminating errors in positioning that aren't absolutely necessary, the parts can be machined using a technique known as the tool concentration process. This involves using a single tool to machine all of the parts that can be worked on in a single clamping, and then switching to a different set of parts. Another knife to be used in the machining of other components. In this manner, the number of tool changes as well as the idle time that occurs between them can be cut down, which in turn helps to eliminate unnecessary positioning errors.
According to the processing part sequence method, each part has a unique structure and shape, and the technical requirements of each surface are also distinct. Because of this, the positioning methods that are used during processing are also milling parts online distinct, and the process can be segmented according to the various positioning methods. In the case of components that require a significant amount of processing, the processing part itself may be subdivided into multiple parts based on the structural characteristics of the constituent parts, such as inner shape, outer shape, curved surface or plane, etc. In most cases, the plane and positioning surface are processed first, followed by the hole; the simple geometric shape is processed first, followed by the complex geometric shape; and the hole is processed after the simple geometric shape. The components with the lowest level of precision are processed first, followed by the components with the highest level of precision.
When dividing the process according to the machining accuracy, stiffness, and deformation of the parts by the roughing and finishing sorting method, the process can be divided according to the principle of separating the roughing and finishing, which is to say, roughing first and then finishing. This allows the process to be divided according to the machining accuracy, stiffness, and deformation of the parts. Processing can be done with the machine tool or with a variety of other tools; for parts that are prone to machining deformation, due to the deformation that may occur after rough machining, it is necessary to correct the shape. Because of this, the process should generally be separated for rough and finish machining.
- Sanat
- Doğa
- El sanatları
- Dans
- İçecekler
- Film
- Kondisyon
- Gıda
- Oyunlar
- Bahçıvanlık
- Sağlık
- Ev
- Edebiyat
- Müzik
- Networking
- Diğer
- Parti
- Din
- Alışveriş
- Spor Dalları
- Tiyatro
- Yaşam