During the course of the production of a large number of distinct types of mechanical componentsWhat
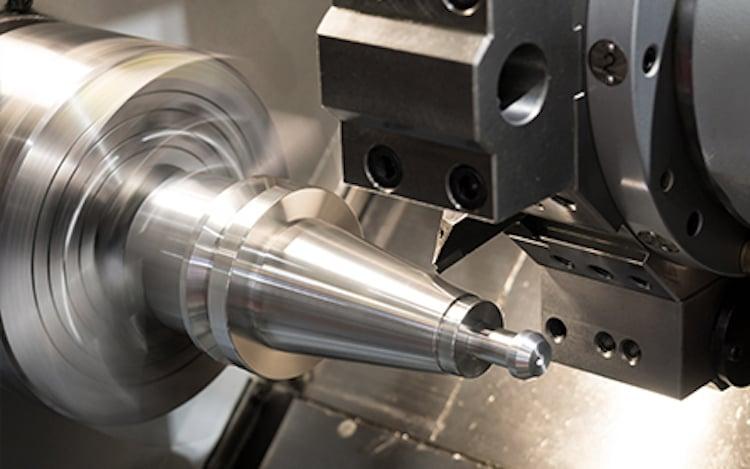
When this particular requirement has been met, only then can we consider the CNC Prototype Machining task to have been successfully completed and moved on to the next step. Visual inspection to determine whether or not the surface of the machined parts have been damaged, rusted, or bruised; to determine whether or not the thread shape and angle are correct; and to determine whether or not the finish of the machined parts satisfies the specifications of the drawing. It is of the utmost importance to maintain detailed records in order to use them in the future in the event that any of the problems that have been outlined above are found to exist. Comparisons of the material, specifications, and quantities of the parts that are being processed at any given time are made with great care to ensure that they are in accordance with the drawings throughout the entirety of the manufacturing process. In addition, each individual component will be checked while the process is being carried out, and then it will be checked again to ensure that the results are accurate. At each and every stage of the process, the assembly must be carried out in a manner that is in full and complete conformity with the regulations and procedures specified by the final assembly drawings. This must be done in a way that is in full and complete conformity with the regulations and procedures specified by the final assembly drawings. It is of the utmost significance to ensure that exhaustive records are kept up to date throughout the entirety of the process of quality acceptance.
When performing a specific kind of processing, there is a specific order in which the various processing steps have to be carried out, and it is imperative that this order be adhered to at all times.
When this particular requirement has been met, only then can we consider the task to have been successfully completed and moved on to the next step. Visual inspection to determine whether or not the surface of the machined parts have been damaged, rusted, or bruised; to determine whether or not the thread shape and angle are correct; and to determine whether or not the finish of the machined parts satisfies the specifications of the drawing. It is of the utmost importance to maintain detailed records in order to use them in the future in the event that any of the problems that have been outlined above are found to exist. Comparisons of the material, specifications, and quantities of the parts that are being processed at any given time are made with great care to ensure that they are in accordance with the drawings throughout the entirety of the manufacturing process. In addition, each individual component will be checked while the process is being carried out, and then it will be checked again to ensure that the results are accurate. At each and every stage of the process, the assembly must be carried out in a manner Investment Castings that is in full and complete conformity with the regulations and procedures specified by the final assembly drawings. This must be done in a way that is in full and complete conformity with the regulations and procedures specified by the final assembly drawings. It is of the utmost significance to ensure that exhaustive records are kept up to date throughout the entirety of the process of quality acceptance.
When performing a specific kind of processing, there is a specific order in which the various processing steps have to be carried out, and it is imperative that this order be adhered to at all times.
The maximum capacity for the number of products that can be produced is largely determined by the level of precision that can be achieved through the machining process. This plays a significant role in the determination of the maximum capacity. This is a rule that CNC prototyping processes cannot be broken in any way. This is a rule that must be followed at all times and in any circumstance. Investigating the role that the component plays in the system is the most effective way to get an answer to this question because doing so will reveal the purpose that the component was designed to fulfill. This procedure is carried out an infinite number of times until the predetermined standard has been attained. This process will be repeated an infinite number of times until the desired level of quality has been achieved. It is possible to reach the required standard by employing the adjustment method, which entails making an initial adjustment to the relative orientation of the machine tool, the fixture, the workpiece, and the tool. In order to do so, the standard must be met. Because of this, it is possible to achieve compliance with the requirements of the standard. To accomplish this objective, all that is required of you is to carefully carry out the directions that have been laid out for you. This is as a result of the fact that selecting the transmission that enables deceleration is a step in the process that bears an incredible amount of significance. This is because the end piece is able to transmit a greater force than any of the other transmission parts, which is the reason for this particular characteristic. This is due to the fact that the end piece is able to transmit a greater force than any of the other components of the transmission combined.
When there are multiple processes that are halted in the same device, the order of the processes should be determined by which one causes the workpiece to suffer the least amount of rigid damage. When there are multiple processes that are halted in the same device, the workpiece should be rigidly damaged. When multiple processes are halted in the same device, the workpiece should be damaged in a manner that is both rigid and severe. This is the best way to ensure that the workpiece is damaged. When there are multiple processes that are halted in the same device, the tool centralized sorting method involves dividing the process in accordance with Copper CNC Machining the tools that are being used, and then using the same tool to process all of the parts on the part that can be finished. This method is utilized when there are multiple processes that are halted in the same device. This technique is the one that is used to deal with situations in which multiple processes that were being executed on the same piece of hardware have all come to a halt at the same time.
This tactic is predicated on the assumption that the process as a whole can be completed in a shorter amount of time if each of the component's parts is worked on using the same instrument. completing the remaining tasks by making full use of the capabilities possessed by each knife, with the goal of maximizing the use of the second and third knives to the full potential of their use in order to maximize the effectiveness of using those knives. When working with components that require a significant amount of processing, there is always a chance that something similar will take place. If you are looking for a professional manufacturer that specializes in CNC processing, Xiaobian recommends that you base your decision on a number of criteria. If you are interested in purchasing one of these services, Xiaobian suggests that you base your decision on these and other criteria in order to find a reputable CNC processing manufacturer. Xiaobian also includes other criteria in this recommendation. It is recommended by Xiaobian that you proceed in this direction if you want to find what it is that you are looking for.
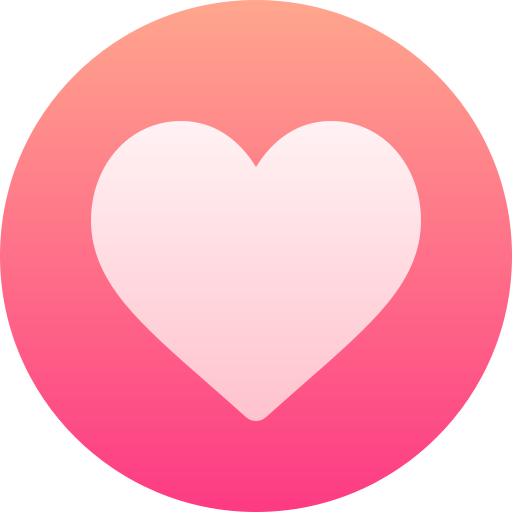
- Art
- Causes
- Crafts
- Dance
- Drinks
- Film
- Fitness
- Food
- Spellen
- Gardening
- Health
- Home
- Literature
- Music
- Networking
- Other
- Party
- Religion
- Shopping
- Sports
- Theater
- Wellness