When working with alloy die-casting mold temperature control machines are required in order to ensure
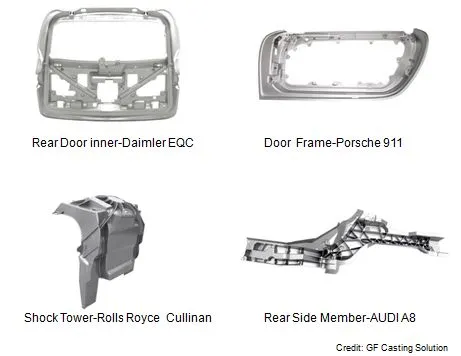
It is clear that the temperature of alloy die zinc die casting is significantly higher than the temperature of other processes in the manufacturing industry when compared to other types of metal castings. The temperature reached during this process is extremely high when compared to the temperatures reached during other processes.
Looking at the various types of aluminum alloy die-casting factories that are currently available on the market, you will notice that die-casting is formed during the manufacturing process when a high-pressure liquid metal is forced into a specific precision metal mold at a rapid rate. In the course of the die-casting procedure, which involves the cooling and solidification of liquid metal under pressure, dies are formed as a result of the process. It is a type of metal casting process that involves the cooling and solidification of liquid metal under pressure, which is known as die-casting. There are two types of common aluminum alloy die-casting processes: cold chamber die-casting and hot chamber die-casting. Cold chamber die-casting is the more common of the two. The cold chamber die-casting process is the more common of the two methods of casting. In comparison to the other two methods of casting, the cold chamber die-aluminum alloy die casting process is the more common. It is more common than either of the other two methods of casting when compared to the cold chamber die-casting process. When comparing the cold chamber die-casting process to the other two methods of casting, it is more common than either of the other two methods. It is more prevalent than either of the other two casting methods when compared to the cold chamber die-casting process.
When comparing the cold chamber die-zinc die castings process to the other two casting methods, it is more prevalent than either of the other two casting methods. It is worth noting that the cold chamber die-casting process, which is currently available in two varieties, is by far the most widely used process in the manufacturing industry, and this should be taken into consideration when developing a process. While the cold chamber die-casting process is discussed in greater depth in this article than either of the other two processes discussed in this article, the cold chamber die-casting process receives the most attention in this article. Because it is the more widely used of the two processes discussed in this article, it merits a greater amount of attention than the other two processes discussed in this article. As a result, this fundamental principle serves as the foundation for the aluminum alloy die-casting process, which is based on the compression principle and is used to form aluminum alloy metal parts. The process is referred to as die casting in the technical literature as a result of this designation.
Following that, a more in-depth discussion of the anodizing procedure will take place. Anodizing, which is typically performed after the formation of aluminum alloy die castings, appears to be widely understood by all parties, according to the information available. Anodizing has the goal of extending the service life of aluminum workpieces while also improving their wear resistance and compressive strength, all while reducing their weight. When it comes to aluminium, remember that the term "anoxication" refers to the anodizing process rather than the finished product; otherwise, the term "anoxication" would be misleading. There are numerous applications for it in the oxidation processing industry, and it can be found in a wide range of different settings. Among those who work in the oxidation processing industry, sulfuric acid is a common electrolyte. Specifically, it is employed in this industry as a support material in the electrolysis process, where it assists in the electrolysis process. A significant contribution to the efficiency of the processes that take place in these facilities comes from the use of sulfuric acid, which is used to accelerate the process as it takes place. As a result of the sulfuric acid-induced anodic oxidation of aluminum alloy die castings (SAAOD), this phenomenon is known as sulfuric acid-induced anodic oxidation of aluminum alloy die castings (SAAOD). It is described as a process in which sulfuric acid is used as a catalyst on the surface of aluminum alloy die castings in order to form an anodic oxide film on the surface of aluminum alloy die castings. The anodic oxide film formed on the surface of aluminum alloy die castings is used to protect the aluminum alloy die castings from corrosion.
According to the International Die Casting Association, automotive and motorcycle parts account for approximately 48% of total die China die casting mold output, with mechanical equipment components accounting for an additional 12% of total die casting output. Household appliances and three-dimensional products (which account for 11% of total output) and three-dimensional products (11% of total output) are two other categories of die casting output, in addition to daily necessities (which account for 28% of total output). Aside from the industries and applications previously mentioned, die castings are used in a wide variety of other industries and applications in addition to those previously mentioned, demonstrating their adaptability. It has a wide range of applications that are illustrated in the diagram and is capable of being used in a variety of scenarios. In spite of the fact that die casting technology has a number of advantages, it also has a number of drawbacks that outweigh any of the numerous advantages that the technology has to offer. It is true that die casting technology has many advantages, but it also has a number of drawbacks that outweigh the numerous advantages that it has to offer. On the one hand, new technologies aimed at improving the quality of die-casting parts are constantly being developed in response to the problems that exist in the die-casting process. On the other hand, new technologies aimed at improving the quality of die-casting parts are constantly being developed in response to the problems that exist in the die-casting process. Meanwhile, in response to the problems that exist in the die-casting process, new technologies aimed at improving the quality of die-casting parts are being developed on a continuous basis. Meanwhile, new technologies aimed at improving the quality of die-casting parts are being developed on a continuous basis in response to the problems that currently exist in the die-casting process. New technologies for improving the quality of die-casting parts are being developed on a continuous basis, in response to the problems that currently exist in the die-casting process, and are being introduced into the market. Continual research and development is underway to improve the quality of die-casting parts in response to the problems that currently exist in the die-casting process. These technologies are being introduced into the market as they are developed.
In response to the problems that currently exist in the die-casting process, ongoing research and development is being carried out to improve the quality of die-casting parts on a continuous basis. As new technologies are developed, they are being introduced into the market in a phased manner. A continuous program of research and development is being carried out in response to the problems that are currently present in the die-casting process in order to improve the overall quality of die-casting parts on a continuous basis. In order to accommodate the development of new technologies, they are being introduced into the market in a phased manner. To address the issues that are currently present in the die-casting process and to continuously improve the overall quality of die-casting parts, a continuous program of research and development is being carried out in response to the problems that are currently present. Because new technologies are being introduced into the market in stages to allow for development, they are being introduced into the market in phases. Earlier in this article, it was stated that the implementation of control technology for die-casting formability is being developed as a response to problems that have arisen during the die-casting process. This statement has been confirmed. The development of some new die-casting technologies that are distinct from traditional die-casting technologies but related to them in terms of process inheritance, in order to capitalize on the unique characteristics of modern die casting manufacturer that are distinct from traditional die-casting technologies but related to them in terms of process inheritance, in order to capitalize on the unique characteristics of modern die-casting technologies that are distinct from traditional die-casting technologies but related to them in terms of process inheritance, in order to capitalize on the unique characteristics of modern die-cast
Because of the ability to manufacture products at extremely high levels of efficiency while also producing products at exceptionally high levels of product quality, both productivity and product quality increase, which is beneficial to both the manufacturer and the consumer. Using this technique, it is possible to improve not only the dimensional accuracy of finished products, but also the overall productivity of finished products as well as the overall quality of finished products. This is because castings solidify in a relatively short period of time at a low temperature with minimal solidification shrinkage. This holds true for both the overall productivity of finished products and the overall quality of finished products.
In addition to lowering production costs while also conserving resources to the greatest extent possible, it has already been stated that achieving the third goal is essential.
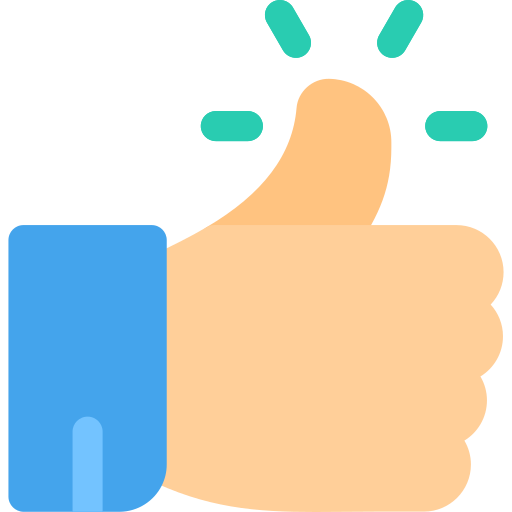
- Sanat
- Doğa
- El sanatları
- Dans
- İçecekler
- Film
- Kondisyon
- Gıda
- Oyunlar
- Bahçıvanlık
- Sağlık
- Ev
- Edebiyat
- Müzik
- Networking
- Diğer
- Parti
- Din
- Alışveriş
- Spor Dalları
- Tiyatro
- Yaşam