How to determine which connection method is best suited for carbon fiber composite materials
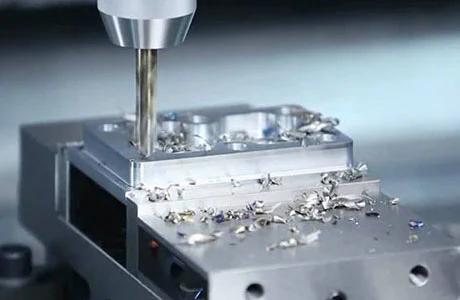
In the production of a large number of distinct kinds of mechanical apparatus, it is common practice to make use of components that are made from carbon fiber composite materials. A few examples of the various types of machinery that fall under this category are airplanes, automobiles, rail vehicles, robots, and others. Connections made with carbon fiber composite materials and other types of components, as well as connections made between carbon fiber composite materials themselves, typically take one of three forms: either a hybrid connection, a mechanical connection, or a glue connection. Hybrid connections are those in which two or more different types of connections are used. This holds true not only for the relationship between carbon fiber composite materials, but also for the materials themselves.
1. It is recommended to use mechanical connection for components whose thickness, length, or overall volume account for a large proportion of the entire equipment. 2. It is recommended to use mechanical connection for components whose thickness, length, or overall volume account for a large proportion of the entire equipment2. It is recommended to use a mechanical connection for components whose thickness, length, or overall volume account for a large proportion of the entire equipment. Citation needed
This is due to the fact that during operation, heavier or larger pieces of mechanical equipment frequently produce higher levels of vibration and friction than their smaller or lighter counterparts.Connection because, in comparison to the mechanical connection, the way of gluing makes it not only simple to obtain a smooth transition shape that satisfies the requirements of aerodynamics, but also, and this is of the utmost importance, it will not significantly increase the dead weight of the body. Dead weight is a factor that affects small equipment, particularly precision equipment.It has a significantly larger surface area in comparison to mechanical connections, but its reliability is significantly lower due to the nature of the connection.
2. After making your selection, determine whether or not the components need to be disassembled in order to cnc machining services be replaced or reassembled, and then base your decision on the information that you uncovered in step two.
In this case, the establishment of a mechanical connection is accomplished through the application of metal in addition to composite materials comprising carbon fiber.After the worn-out connection part has been replaced, the procedure that can be described as being relatively straightforward is the process of conducting regular checks.It is difficult to make an accurate prediction and check the quality of the joint in time to prevent the joint from being completely destroyed. This is necessary in order to prevent the joint from being completely destroyed.
3. Determine the stress levels and the sealing requirements for the joint by using the components as a guide, and then calculate the stress levels. In addition to this, whenever the joint is adjusted, additional stress will be produced, and it will be necessary to carry out secondary sealing for the hole. Connecting bolts are an additional component that are essential to achieving a successful outcome in the mechanical connection. When utilizing the cemented connection method, you won't run into any difficulties with regards to the concentration of stress or the prevention of corrosion. This is because there are no entrances or exits provided by the method.
When compared to the method of a single connection, the method of a hybrid connection, which combines cementation and machinery, is the one that sees the most widespread application because of its combination of the two. This is due to the fact that the hybrid connection method combines both cementation and machinery. In addition to a plethora of other benefits, advantages include a low body weight, high strength, resistance to fatigue and creep, and so on.
In the production of a large number of distinct kinds of mechanical apparatus, it is cnc machining service common practice to make use of components that are made from carbon fiber composite materials. A few examples of the various types of machinery that fall under this category are airplanes, automobiles, rail vehicles, robots, and others. Connections made with carbon fiber composite materials and other types of components, as well as connections made between carbon fiber composite materials themselves, typically take one of three forms: either a hybrid connection, a mechanical connection, or a glue connection. Hybrid connections are those in which two or more different types of connections are used. This holds true not only for the relationship between carbon fiber composite materials, but also for the materials themselves.
1. It is recommended to use mechanical connection for components whose thickness, length, or overall volume account for a large proportion of the entire equipment. 2. It is recommended to use mechanical connection for components whose thickness, length, or overall volume account for a large proportion of the entire equipment2. It is recommended to use a mechanical connection for components whose thickness, length, or overall volume account for a large proportion of the entire equipment. Citation needed
This is due to the fact that during operation, heavier or larger pieces of mechanical equipment frequently produce higher levels of vibration and friction than their smaller or lighter counterparts.Connection because, in comparison to the mechanical connection, the way of gluing makes it not only simple to obtain a smooth transition shape that satisfies the requirements of aerodynamics, but also, and this is of the utmost importance, it will not significantly increase the dead weight of the body. Dead weight is a factor that affects small equipment, particularly precision equipment.It has a significantly larger surface area in comparison to mechanical connections, but its reliability is significantly lower due to the nature of the connection..
2. After making your selection, determine whether or not the components need to be disassembled in order to be replaced or reassembled, and then base your decision on the information that you uncovered in step two.
In this case, the establishment of a mechanical connection is accomplished through the application of metal in addition to composite materials comprising carbon fiber.After the worn-out connection part has been replaced, the procedure that can be described as being relatively straightforward is the process of conducting regular checks.It is difficult to make an accurate prediction and check the quality of the joint in time to prevent the joint from being completely destroyed. This is necessary in order to prevent the joint from being completely destroyed.
3. Determine the stress levels and the sealing requirements for the joint by using the components as a guide, and then calculate the stress levels. In addition to this, whenever the joint is adjusted, additional stress will be produced, and it will be necessary to carry out secondary sealing for the hole. Connecting bolts are an additional component that are essential to achieving a successful outcome in the mechanical connection. When utilizing the cemented connection method, you won't run into any difficulties with regards to the concentration of stress or the prevention of corrosion. This is because there are no entrances or exits provided by the method.
When compared to the method of a single connection, the method of a hybrid connection, which combines cementation and machinery, is the one that sees the most widespread application because of its combination of the two. This is due to the fact that the hybrid connection method combines both cementation and machinery. In addition to a plethora of other benefits, advantages include a low body weight, high strength, resistance to fatigue and creep, and so on.
After subjecting the magnesium alloy to a heat treatment and creating a metallographic sample, the microstructure is analyzed and then compared to a photograph of the standard microstructure. This process is repeated until a conclusion is reached. Because of this, it is possible to evaluate the effectiveness of the heat treatment that was performed on the magnesium alloy. The primary factors that are evaluated during the inspection are the grain size of cast and deformed alloys, coarse compounds in extruded, forged, or rolled alloys, voids and molten pores in cast alloys as a result of improper solid solution treatment, and coarse compounds in magnesium alloys that have been cast. Among these are the benefits of high production efficiency, the conservation of raw materials, the reduction in production costs, as well as good product performance and high precision offered by the processing technology for aluminum-magnesium alloys. This is because it is a more advanced method of processing that requires significantly less cutting than traditional methods. When it comes to the components that make up Huiwen Zhizao, the quality inspection standards are extremely demanding due to the nature of the product.
The hardness test has many benefits, some of which are its speed, its ease of use, and custom cnc milling its capability of being carried out directly on the heat-treated workpiece, without the requirement of using special samples. Another benefit of the hardness test is that it can determine the workpiece's hardness without the need to use special samples. The majority of the time, the tests for Brinell and Rockwell hardness are the ones that are carried out. Case in point Case in pointOn the other hand, the Rockwell surface hardness test is sometimes used for workpieces that are made of magnesium alloys and have a thin section. This is because the Rockwell test measures how hard the surface of the material is. In order to obtain the most accurate results possible from a test, it is recommended to use a Brinell hardness tester on magnesium alloys with larger grains and a lower hardness. This will allow one to obtain the most accurate results possible.
The value that was measured for the material's hardness is only used as a parameter for the purpose of judging the efficacy of the heat treatment that was applied to magnesium alloys. The purpose of this evaluation is to determine how effective the heat treatment was. This is because the strength index that is proportional to the degree of hardness varies quite a bit from one instance to the next. The reason for this is that the level of hardness affects the strength index. However, the specimens that are cast separately and are not machined are the ones that are typically used. This is because the specimens that are obtained after machining castings made of magnesium alloy are more representative of the actual properties of the castings. In spite of the fact that the specimens obtained after machining the castings have a higher degree of accuracy, this is still the case. It is necessary, in the vast majority of instances, for the tests to be carried out in a fashion that is consistent with the standards that have been established by the ASTM in order to guarantee that the results of the tests are accurate.
- Art
- Causes
- Crafts
- Dance
- Drinks
- Film
- Fitness
- Food
- Games
- Gardening
- Health
- Home
- Literature
- Music
- Networking
- Other
- Party
- Religion
- Shopping
- Sports
- Theater
- Wellness